STEEL PRE-HEATING OVEN ROOM
-
TB-EKOSYSTEM Individually controlled top and bottom steel pre-heaters heat the steel to the correct temperature prior to the application of the polyurethane.
-
The section includes electrical heating with automatic control to allow heating to 40 degrees +/- 2 degree accuracy from 10 degrees ambient.
PRIMER DOSING AND DISTRIBUTION SYSTEM
-
TB-EKOSYSTEM Low pressure machine includes in its equipment all the technical user-friendly solutions to guarantee long life and the best mixing quality
-
The machine is managed by an electrical cabinet c/w PLC, the software guarantees a continuous control of the foaming cycles and of the alarm signals of the critical parts of the machine; the flow rates, the temperatures, the daily tank levels, the head cleaning cycles, the daily tanks filling from storage tanks are always monitored by the software installed in the machine and shown on the "touch screen" operator panel
Mixing Head TRAVERSE
-
TB-TB-EKOSYSTEM Mixing Head Traverse is composed of: Electro-welded machined steel portal structure, accommodating the mixing head holder traverse.
-
The portal can longitudinally slides as to the metal sheet forward, by means of a moto-reducer.
-
This movement ensures the shifting in case of a sudden stop of the line, so avoiding the head to be covered by the blowing foam.
-
The movement is through parallel rails clamped to the floor;
Traverse with guides for mixing head, composed of a trolley installed in the system with linear guides, and driven by brushless motor with belt transmission.
-
This traverse can be adjusted in height, and the movement is through motorised screws;
High pressure pneumatic pump to wash the head, that automatically engages when the head is in washing position;
it can be manually driven on operator's demand;
Control panel accommodating the working controls of the unit, so to permit the operator to check and to adjust the productions parameters.
he first calibration is carried out on the main panel.
TB-EKOSYSTEM Main Components Metering Line
- Composed of Rotary Power or Rexroth Axial piston pump;
- Three phases electric motor servo ventilated with magnetic coupling;
- Electronic digital pressure gauge 0-40 bar on the suction line;
- Electronic digital pressure gauge 0-400 bar on the feeding line with analogue signal 4-20 mA;
- Self-cleaning filter with automatic cycle;
- Automatic control of the temperature with plate-made heat exchangers for polyol and MDI, to be connected to a chiller ensuring a working temperature adjustable from +17°C to 28°C, with +/- 1°C precision (medium working temperature: +22°C);
- Automatic valve for recycle cycle with limit switch to check the right position of the valve;
- +/-1% metering accuracy checked by Endress & Hauser mass flow meters;
- The pumps work in close loop with motor speed variation by inverter to have the auto regulation of the output in real-time.
TB-EKOSYSTEM 1 off CATALYST & ADDITIVE HIGH PRESSURE METERING MODULE
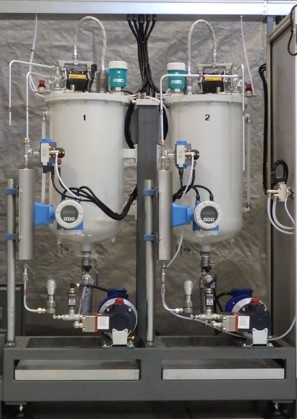
- Min and max output of CATALYST : min 0,06 max 0,5 Kg/minute
- Min and max output of ADDITIVE : min 0,025 max 0,3 Kg/minute
- Catalysts & Additive tank c/w capacitance level control, loading valve with actuator managed by PLC,
- The tank is equipped with 1/2" diaphragm-operated pump for the loading from drums.
- 0.5 bar pressurisation with certificate safety valve for catalyst & Additive tank.
- Metering pump with unit driven by converter, to change the delivery from operator panel, +/-1% metering accuracy checked by mass flow meters.
- Mass flow meter to take the flow-rate and working consumptions automatically
- Digital pressure gauge sited at metering pump feed port, with safety alarms, and analogical signal to visualise the working pressure on the monitor.
- metering pump for Catalyst & Additive, having three pumping heads, and with changeable delivery from min 0.06 kg/1' and max 0.5 kg/m for Catalyst, min 0.025 kg/m and max 0.3 kg/m for Additive, 180 bar working pressure, Hydracell type.
TB-EKOSYSTEM 1 off PENTANE High Pressure Metering & Safety System
- The Pentane module system is equipped with all those devices making it suitable as per ATEX 94/9 standards in force
- The line is composed of:
Automatic loading valve with closing in case of alarm
Stainless steel pipes and fittings for the connection to the metering group.
1 off metering pump for pentane, having three pumping heads, and with changeable delivery from min 0.4 kg/min and max 2,2 kg/min, 180 bar working pressure, Hydracell type.
Metering pump drive with unit driven by converter, to change the delivery from operator panel.
Atex digital pressure gauge sited at metering pump feed port, with safety alarms, and analogical signal to visualise the working pressure on the monitor.
Atex mass meter to take the flow-rates and working consumptions automatically.
3-way manual valves for flow-rate control.